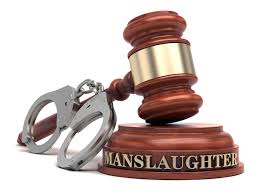
In Victoria, from July 1 this year, the consequences of a workplace fatality will become far more serious for employers who are not providing a safe workplace. This date marks the passing of the Workplace Safety Legislation Amendment Bill 2019 – Workplace Manslaughter into law.
The Victorian Parliament has created Australia’s highest safety fine and made Victoria the third Australian jurisdiction to make industrial manslaughter a criminal offense.
Where are the new laws & Who so the laws apply to?
The new industrial manslaughter laws have been added to the Victorian Occupational Health and Safety Act 2004 (Vic) (OHS Act) and will apply to employers, designers, manufacturers, self-employed persons as well as officers. The laws apply to all businesses irrespective of size.
The new laws will introduce maximum fines of approx. $16.5m for employers and jail terms of up to 20 years and fines of up to $1.65m for officers whose actions or omissions:
- cause the death of a worker or member of the public;
- involve a breach of an OHS duty;
- were negligent
Where there are principle contractors and contractors involved in a workplace they will both have duties and they will be identified on a case by case basis.
The accused must be/or circumstances must involve:
- A body corporate and not a person who is an employee or volunteer
- Must owe a duty pursuant to sections 21-24 & sections 26-31 of the OHS Act 2004
- Must have breached the duty with a criminal offence where there is a high risk of death or injury
- The act causing the death must have been carried out consciously
- There must be a death
How is negligence defined?
The negligence standard is the criminal negligence standard and applies where there is a great falling short of the care that would have been taken by a reasonable person in the circumstances in which the conduct was engaged in, and involves a high risk of death or serious injury or serious illness.
Who is an Officer?
An officer – Defined on a case by case basis. Typically a person who has the means to affect a safe work culture via day to day control over work processes and resources. An officer is typically somebody senior in the business must have a contribution to the significant company decisions.
What should businesses do now?
It is important to note that if you comply with the legislation now you will comply after July 1 the new laws are an increase in consequence change not a duty change and all existing laws pre 1st July 2020 will still apply post 1st July 2020.
However, it is important for businesses that they continued to ensure adequate OHS systems, instruction, training, supervision and also place a heavy focus on worker engagement and a strong safety culture within the organisation.
Now is a good time to review your organisations workplaces and processes. The steps you should look at taking include:
- Reviewing all the potential hazards and risks in the workplace and ensuring that these risks are assessed and controls implemented.
- Completing a formal review of all the safety systems and controls currently in place and ensure they are fully effective
- Reviewing OHS leadership and culture to ensure that any alleged negligent conduct is not authorised or permitted by the company or culture;
- Education and awareness for directors, senior officers and managers on the new legislation and offences;
- Reviewing incident action plans and responses
- Self-employed persons must consider how their business effects the safety people
- Designers and manufacturers must design and make safe equipment
Posted By: Cathal Uniacke – cathal@custodiansafety.com.au